Injection molding is an art, which involves science as well. Actually, injection molding requires great attention to detail as minor mistakes can cause a lot of financial loss to a company. In this article, we are going to discuss how you can eliminate common injection molding defects.
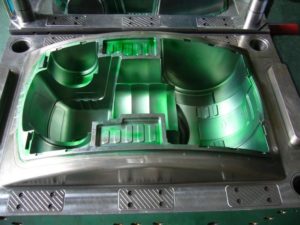
Flow Lines
Flow lines may include lines, patterns, and streaks that appear on the prototype part because of the cooling profile or physical path of the molten plastic while it moves into the cavity.
Fix:
- One way to fix the issue is to increase the pressure and injection speed, which will make sure that the mold will fill the cavities.
- Another way is to round the locations and corners where the thickness of the wall changes.
Sink Marks
These are minor depressions or craters that form in the thicker areas when shrinkage happens in the internal areas of the end product.
Fix:
- Reduce the mold temperature, increase the holding pressure and time for better curing and cooling.
- Reduce the thickness of the wall sections that are the thickest. This will allow faster cooling and prevent the sink marks.
Vacuum Voids
Vacuum voids refer to the air pockets inside or near the prototype surface. They occur because of the uneven solidification amidst the inner sections and the surface.
Fix:
- Find the gate at the mold’s thickest part
- Opt for the plastic that is less viscous, which will reduce the amount of gas trapped.
- Increase the holding time and pressure
- Try to keep the mold parts aligned
Surface Delamination
Surface delamination happens when thin layers of the surface show up on the part because of a contaminant. Actually, these layers look like coats that can be peeled off.
Fix:
- Before molding, make sure you dry the plastic properly
- Raise the degree of mold temperature
- There should no sharp turns and corners in the mold design
Weld Lines
Weld lines show up on an area where the liquid plastics mixes while they flow from different injection mold parts.
Fix
- Increase the temperature of molten plastic or mold
- Raise the injection speed
- Make adjustments to the design to ensure that the flow pattern is only one source flow
Short Shot
Short shot refers to a situation that happens when a molding shot tends to fall short. In other words, the molten plastic won’t fill the cavity of the mold for some reason. As a result, it leaves a portion where you can see plastic.
Fix
- Opt for a plastic that features higher flow and less viscosity
- Raise the mold temperature for better flow
- Get a machine that features more material feed
To cut a long story short, you may have to face a lot of defects during the process of injection molding in China. What you need to do is follow the tips given in this article to fix or eliminate these issues to make the process error free. Hopefully, you will find these tips helpful.
Resource box: This article is originally posted in https://www.injectionmouldchina.com.