Here is the brief introduction of china high precision molds.
Draft
Draft alludes to the point of slope set between the vertical surfaces of the plastic moldings and the shape opening course. Draft is ordinarily applied to encourage discharge of the moldings from the shape. Item creators as often as possible stay away from the use of noteworthy draft, since it changes the tasteful type of the structure and lessens the embellishment’s inward volume. All things considered for products made by injection moulding china, draft is generally applied to plastic moldings to maintain a strategic distance from launch issues and incredibly complex shape plans.
Draft edges on ribs must be painstakingly indicated. In the past rib configuration, for example, a 2° draft point was applied to encourage the launch of the formed part from the shape. Regarding item usefulness, a lesser draft point might be wanted since this takes into consideration taller and thicker ribs with more prominent solidness.
Lamentably, lower draft points, (for example, % or 1°) may make the part unreasonably stick in the form. This issue of staying upon part launch can be intensified when shaping with mica-and additionally glass filled materials that have low shrinkage and high surface harshness. All things considered, the passable draft point is an unpredictable capacity of the material conduct, handling conditions, and surface completion.
A base draft point of 0.5° is regularly utilized, with 1 to 2° ordinarily applied by material provider proposals. Unpleasant and finished surfaces ordinarily require extra draft, with an extra 1° of draft regularly applied per 20 1um of surface unpleasantness or surface profundity. Table 2.3 gives some prescribed draft edges to a couple of various surface completions and materials; the suggested draft point increments with the surface harshness. Concerning the material properties, the draft point should increment for glas-filled as well as low shrinkage materials yet might be diminished for exceptionally adaptable materials, for example, delicate PVC.
Undercuts
An undercut is an element in the item structure that meddles with the launch of the embellishment from the shape. These structure highlights incorporate, for instance, a window in a side divider, a shade over the base mass of the section, a flat chief, and a snap bar or”finger.”
To give some knowledge into why these highlights are normally dodged by high precision plastic injection mould suppliers, consider three diverse however basic form structure procedures for embellishment a snap pillar with the shape shut before discharge and with the moving side withdrew and the ejectors reached out forward. Since the snap shaft is smaller at its neck than at its tip, there is an undermined in the shape that the form architect must know about and make the plan with the end goal that the part can be launched out after the shape opens. If it’s not too much trouble note that the gave plans are not planned to recommend the utilization of each of the three techniques in a solitary shape, yet just give a premise to conversation.
The plan at the left is the least complex of the three, wherein an opening or window at the base of the snap pillar permits a distension from the fixed side to center, out the territory pit underneath the undercut. This is a solid procedure, however leaves a gap in the part that changes its capacity and style.
At structure at the privilege is likewise normal, which utilizes an ejector pin with a profiled or shaped surface on its side adjoining the snap shaft. This shaped profile on the ejector pin gives a smaller than normal hole to permit the trim of the top of the pin. At the point when the form is opened and the ejectors are broadened, the pin and part will move together until the part completely clears the shape hole and can free the range from the undercut. When utilizing formed ejectors, a dowel pin or some other structure include must be utilized to keep up legitimate direction of the shaped surface as for the shape hole. Something else, the pit surfaces would not adjust and blemished parts would happen.
The plan at the middle is likewise a typical structure in which a sliding, calculated pin or”lifter” is utilized to center out the volume of the form caught underneath the undercut. After the shape is opened, the progress ahead of the lifter following up on the slanted surface of the form makes the lifter move along the side, accordingly clearing the undercut upon discharge. There are three issues related with lifters that the plastic part and form planner ought to consider while embracing their utilization. In the first place, there is the additional plan time and intricacy used to execute the structure. Second, there is the potential for wear, staying, and expanded support related with the sliding surfaces on the slider itself, on the form surfaces, and inside the ejector get together. Third, the utilization of the lifter requires sufficient leeway between highlights inside the shaped part. As showed, this specific structure likely doesn’t give adequate leeway, to such an extent that the lifter will meddle with the furthest right snap pillar if the lifter is additionally expanded.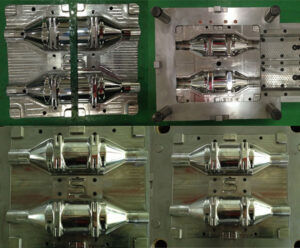
It might appear that such complexities in form configuration would direct the shirking of snap shafts, yet practically speaking, such structures are not generally hazardous for experienced shape creators. More testing than such undermining highlights is the level supervisor that is arranged inside to the part and planned with a shaped inner string. Together, these structure highlights would require a confused form plan with planned activation of different centers before discharge of the item. On the other hand, a”lost core”could be utilized in which the shape center that frames the inside highlights of the part is dissolved away after the part is formed.
Whenever the situation allows, these kinds of item configuration highlights ought to be kept away from since complex shape instruments must be structured and machined for framing and catapulting the formed part. These extra shape parts can make the form more hard to utilize and even harm the form whenever utilized inappropriately. Thus, the form configuration designer ought to distinguish risky highlights, alert the client, and work with the item configuration specialist to expel the undermines. Be that as it may, such undermines ought not be planned out of the item if the capacity gave by the feature(s) with the undercut is indispensable to the item or the expulsion of the undercut would require extra post forming tasks or the upgrade of a solitary part into various pieces.
This article is from www.injectionmouldchina.com.