When it comes to plastic injection molding, manufacturers have a lot of problems and difficulties to deal with. Manufacturers use plastic for many reasons, such as design flexibility, affordability, and lightweight, just to name a few. Making parts and designs with injection molding has some difficulties. Let’s take a look at them.
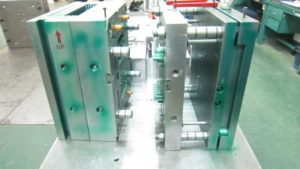
During the injection molding process, you may have problems, such as parts deformation, structural weakness, surface blemishes, warpage, shrinkage, parting lines, voids, and air traps, to name a few.
All these problems may add to the cost of manufacturing. For streamlining the process, you have to use the trial-and-error prototyping process in a virtual environment.
Making tools that can help make high-quality injection-molded parts requires you to consider a lot of variables. For instance, it includes the optimal temperatures of the plastic, cooling channels, and the configuration of these systems, to name a few. Aside from this, you also need to consider pressure, flow rate, thermoplastic material type, solidification time, and so on.
If you have the required mold-filling simulation, you can easily balance the design against manufacturability. Moreover, mold makers can choose to optimize tools without the need for prototype molds. This way the manufacturers can also reduce run cycles, which results in better quality, reduced costs, and less time consumption.
Actually, the primary factor that you need to keep in mind in order to avoid the traditional problems associated with plastic injection molding is the accuracy of simulations.
Evaluating Manufacturability
With plastic injection molding simulation, designers can get answers to common questions related to part filling, air traps, voids, and gate locations, to name a few. With the help of these analyses, designers can perform the simulation of the mold-filling stage in order to understand whether it can speed up the tooling design and production process.
Optimization of the Mold Design
The primary goal of a Chinese mold maker is to develop injection molding tooling that can produce quality parts without costing a lot of money. Moreover, this simulation offers extra tools to optimize tooling designers of different complexity levels. And this helps mold makers simulate different phases like filling and packing.
Improving Cycle Times
It’s really important to reduce cycle times by ejecting quality parts in the shortest time span possible. If advanced capabilities are used, plastic injection molding can help specialists hit the best balance between quality production and short cycle times.
All of this helps the designing and simulating of the cooling line layouts, processing parameter optimization and the making of conformal cooling systems.
Improving Mold-Filling Simulations
Nowadays, manufacturers can enjoy a lot of benefits by molding plastic parts instead of using the traditionally machined parts. For instance, they can reduce costs, scrap, weight and increase the design flexibility via the production of design and shape geometries that are more complex.
However, they can only enjoy these benefits if they boost the design and the productivity of the tooling. Nowadays, manufacturers can improve the performance and efficiency of their operations if they choose to replace or improve the conventional mold using the mold-filling simulations.
So, this was a description of some of the difficulties that manufacturers face during the plastic injection molding process and how these problems can be fixed.
Resource box: This article is originally posted in https://www.injectionmouldchina.com.