Precision Plastic molded parts can be made only by Plastic injection molding. This is the preferred method because injection molding has the advantages of high tolerance precision work.
The following points go into making Precision Plastic molds.
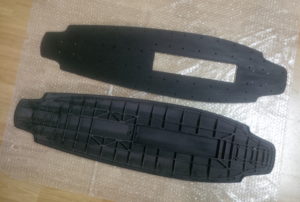
- Using the proper clamping force
Injection molding machine – also known as presses, consist of a material hopper, an injection ram or plunger, and a heating unit. Plastic is injected into the mold through the sprue orifice. These presses are rated by tonnage which is the calculation of the clamping force the press can exert. This force keeps the mold closed while the molding is going on. By rule of thumb, the force needed is determined by the projected surface area of the part being molded. Tonnage can vary from a few to a few thousand. The nature of the material also determines the clamping force. If the plastic is stiff, more injection pressure and more clamping force is needed to keep the mold closed. Also, larger parts require greater clamping forces. These points should be kept in mind when molding.
- Using the proper material for Molds – or die refers to the tooling used to produce the plastic parts by molding. They are expensive to manufacture and were preferred to be used only in large scale production. They are typically constructed from hardened steel, beryllium-copper alloys or aluminum. Steel though expensive, is more long lasting and its high initial cost will definitely be offset by the number of times it can be used. Pre-hardened steel is used for larger parts molding. The mold is heat treated after machining for longer life.
Aluminum Injection Molds cost much less and are used for mass manufacture of small parts. Aircraft quality aluminum is used for making molds. They offer quicker turnaround times because of their high heat dissipation quality. Since they are not wear resistant, they can be coated with fiberglass reinforced material.
Beryllium Copper also is used for quick heat removal especially where the shear heat is more. Shear heat is the phenomenon of heat trapping in a viscous material like melted plastic when the mechanical energy of the plastic granules when they are injected under high pressure is converted to heat energy.
- Using the right Gate
The main enemy of injection molding is stress. The molecules of plastic undergo severe stresses as they are extruded out of the injector into the crevices and corners of the mold to take that shape. They are forced to take sharp corners instead of their natural flow movement. These stresses when the part is cooled get locked into the part and cause warping, cracking, sink marks etc.
Gates are provided at the point of injection to prevent warping. Depending on the shape and size of the part, different types of gates are used.
- State of the art Machining
Using the proper machining to achieve very tight tolerances for their clients molded products. Proper initial designing is very important and can be outsourced to experts on a turnkey project basis. State of the art CNC machining, large boring mills, Blanchard grinding capabilities, conventional EDMs all go into making that perfect precision plastic mold.
Mold manufacturers in China have incorporated these and many more features to produce high quality Chinese molds that are in demand the world over at a fraction of the cost at which they are available in western countries.
For more information, please check out https://www.injectionmouldchina.com.