As far as the plastic molding process is concerned, the injection mold cooling system plays a great role. Actually, this system directly affects the production efficiency, machine speed and the quality of end product. In the case of semi-crystalline polymers and amorphous, the highest level of heat efficiency is required. Let’s know more about this system.
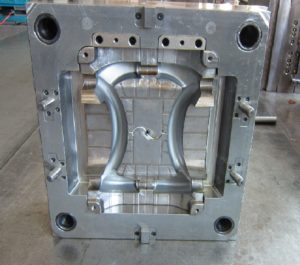
The Design of Injection Mold Cooling Systems
First off, it’s important to keep in mind that the design of this system is of paramount importance. In fact, the cooling time accounts for up to 80% of the cycle. If the cooling system is properly designed, it can reduce the molding time for better efficiency. On the other hand, if this system is poorly designed, the reverse may happen.
So, the question is, what factors should be kept in mind for effective cooling? Given below are some of the major factors.
Plastic wall-thickness
If the plastic thickness is higher, it will take much longer to cool down. As a general rule, the cooling time depends upon the thickness of the parts of plastic. Ideally, it’s better to keep the thickness as low as possible.
It’s possible to choose low thickness, but it may not be possible for all types of projects. So, if the project allows some flexibility, the designers should not go for a higher wall-thickness. This is the number factor on the list.
Mold steel
If the steel has a higher thermal conductivity, more heat can be transferred. As a result, the cooling time will shrink. Typically, China injection mold maker uses copper in place of steel in order to get better results.
The layout of the Cooling line
It’s better to keep the mold cavity near the cooling pipes. Also, it’s better to have cooling pipes with higher diameters for better cooling. Therefore, the designer should consider these parameters in order to enjoy the best cooling effect.
Coolant
As the name suggests, coolants are the things used to cool down the plastic parts. Designers use different types of coolants. The two most common ones are oil and water. In addition, the thermal conductivity and viscosity of the coolant may also have an impact on the heat conduction. If the fluid viscosity is low, the thermal conductivity will be high.
The rules of designing a Cooling system
- Ensuring highest cooling efficiency
- Ensuring consistent cooling in order to avoid deformation of the objects
- Facilitating the process of manufacturing
The goal of the cooling system is to ensure faster dissipation of heat from the objects. This ensures the best physical and dimensional properties. This requires a solid engineering approach in order to measure the injection mold performance with the help of water circuits.
Long story short, this is not a thorough list of factors that should be kept in mind when designing the perfect cooling system for injection molding company in China. However, with the help of this approach and good engineering knowledge, designers can get the best results. This will help them employ the right engineering practices and tools.
Resource box: This article is originally posted in https://www.injectionmouldchina.com.